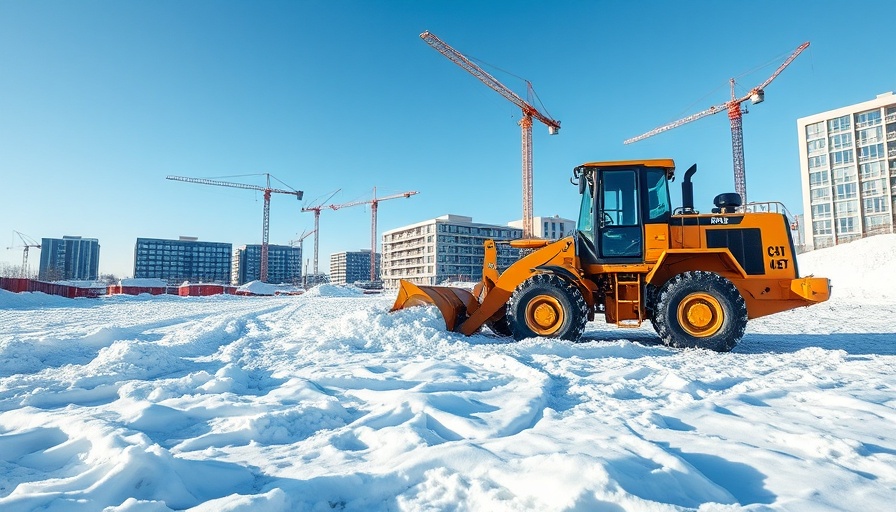
Winter's Hidden Costs: Understanding the Chill Factor
Construction contractors know that winter poses unique challenges, primarily when it comes to budgeting. While snow-covered landscapes might seem picturesque, the cold snap often delivers something far less appealing: substantial losses in productivity, increased material costs, and a slew of maintenance challenges. By understanding these issues ahead of time, construction firms can equip themselves to thrive, rather than just survive, during winter months, saving money while keeping projects on track.
The Effects of Cold on Worker Productivity
Cold weather doesn't just produce chillier air; it can cool down worker morale and productivity. Studies indicate that worker efficiency significantly drops in freezing temperatures. An alarming statistic from 2023 highlighted a 2.2% absence rate due to injuries and illnesses correlated with winter working conditions, translating to a staggering $29.9 billion in lost productivity nationwide.
To mitigate this effect, consider creating heated break areas where workers can warm up and recharge. Furthermore, scheduling outdoor tasks during the milder parts of the day and rotating work crews can keep the job going efficiently while maintaining worker welfare.
Challenge of Maintaining Equipment
In the construction industry, heavy machinery is the backbone of operation, and cold weather can wreak havoc on this essential equipment. Thicker fluids, stalling batteries, and costly repairs due to unmaintained gear can all occur when temperatures drop.
Regular maintenance checks become vital; implementing the use of cold-weather lubricants and antifreeze solutions can cushion machinery against the cold. Additionally, storing hydraulics and machinery indoors or employing thermal covers further protects your assets, reducing the likelihood of time-consuming breakdowns.
Materials Misbehaving in Cold Conditions
Not all materials are created equal, and temperatures can greatly influence their performance. Cold temperatures can lead to poorly curing concrete and paint, facilitating structural failures and necessitating costly rework.
To minimize these risks, keeping materials in temperature-controlled environments and scheduling deliveries to avoid prolonged exposure to cold can safeguard against deterioration. Planning ahead can substantially lower the chances of investing extra resources into remedial work.
Planning for Weather Interruptions
Winter weather often disrupts even the best-laid plans. Snowstorms and icy conditions can lead to project delays, increased labor costs, and scheduling conflicts.
To combat this, it’s crucial to have a detailed action plan that includes contingencies for inclement weather. Being proactive rather than reactive can save headaches down the line and keep both your timeline and budget intact.
Financial Safety Nets: Budgeting for Cold Weather
A well-prepared construction firm anticipates these challenges and budgets accordingly. Setting aside a contingency fund specifically for winter-related expenses can provide a safety net to weather the storms—both literal and financial. This fund can cover costs related to heating equipment, additional labor, or emergency repairs and aid in maintaining a robust budget.
Write A Comment